[193 Pages Report] The Sintering Market size was estimated at USD 1.65 billion in 2023 and expected to reach USD 1.74 billion in 2024, at a CAGR 5.42% to reach USD 2.39 billion by 2030.
Sintering is a manufacturing process that involves compacting and then forming a solid mass of material using heat or pressure without reaching the point of liquefaction. Essentially, this process allows powdered materials to bond and form a solid structure by heating them just below their melting point, usually in a controlled environment. Sintering is commonly used in metallurgy, ceramics, and additive manufacturing to create components with specific shapes and mechanical properties. As industries such as aerospace and automotive seek materials with higher durability, precision, and strength, sintering provides a versatile solution for producing such high-performance components. Sintering processes generally produce fewer emissions and have a comparatively smaller environmental footprint. The efficient use of materials also contributes to waste reduction. However, the limited applicability of the sintering process for only certain types of metals and ceramics can limit market growth. Moreover, achieving uniformity and consistency in sintering can be technically complex and requires precise control over temperature and pressure. Nevertheless, the integration of automation and artificial intelligence in sintering processes could lead to more efficient production lines, reduced human error, and better quality control. Ongoing research into new alloys and composite materials could expand the range of applications for sintering, opening new markets and industries to this technology.
The sintering market in the Americas is driven primarily by robust industrial and manufacturing sectors, particularly in the United States and Canada. The region benefits from advanced technology and innovation in metallurgy and material sciences, leading to higher adoption rates of sintering processes. Key industries utilizing sintering include automotive, aerospace, and medical devices. The presence of leading research institutions and a strong focus on sustainable manufacturing processes also contribute to market growth. Europe's sintering market is characterized by well-established automotive and aerospace industries that demand high-performance and precision-engineered components. Germany, France, and the U.K. are notable landscapes in this market. The region emphasizes environmental regulations and sustainability, which has led to increased research in eco-friendly sintering techniques. Europe also benefits from a strong network of small and medium enterprises (SMEs) specializing in niche markets for sintered products. The region's focus on Industry 4.0 and automation further drives the adoption of advanced sintering processes. In the Middle East, the market for sintering is growing steadily due to rising industrialization and partnerships with foreign companies that bring in advanced sintering technologies. The Asia-Pacific (APAC) region is experiencing robust growth in the sintering market, driven by significant industrialization and urbanization, the presence of a massive industrial base, and government initiatives to boost manufacturing technologies. The automotive, consumer electronics, and machinery sectors are major consumers of sintered products in this region. Additionally, low labor charges and the availability of raw materials further support market expansion.
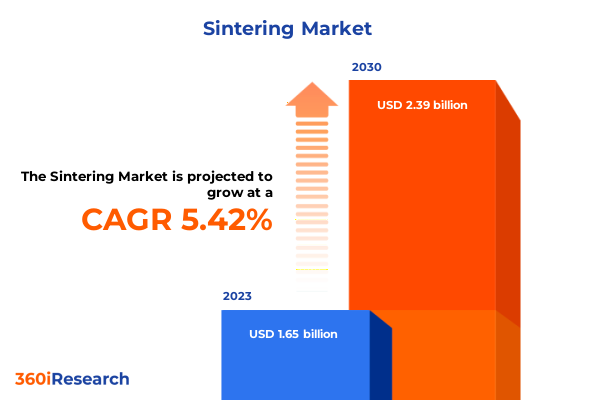
Market Dynamics
The market dynamics represent an ever-changing landscape of the Sintering Market by providing actionable insights into factors, including supply and demand levels. Accounting for these factors helps design strategies, make investments, and formulate developments to capitalize on future opportunities. In addition, these factors assist in avoiding potential pitfalls related to political, geographical, technical, social, and economic conditions, highlighting consumer behaviors and influencing manufacturing costs and purchasing decisions.
- Market Drivers
- Growing demand for lightweight materials in the aerospace and automotive industry
- Increase in ownership of consumer electronics and need for enhanced component performance
- Heightened environmental regulations and adoption of eco-friendly sintering techniques to reduce industrial emissions
- Market Restraints
- Limited applicability and technical issues
- Market Opportunities
- Ongoing innovations in sintering techniques to extend the applicability and efficiency of sintering processes
- R&D initiatives for the development of new, high-performance alloys and potential for the use of sintering technologies
- Market Challenges
- Complexities in the operation of sintering processes and the need for skilled personnel
Market Segmentation Analysis
Material: Wide usage of sintering in metallurgy for the production of powdered metal products
Metals such as iron, steel, aluminum, and titanium benefit from sintering due to the creation of strong, durable, and complex shapes with cost-efficient production. Iron and steel are among the most commonly sintered metals. Sintering involves heating powdered iron or steel just below their melting points to bond the particles together. This method is used to produce complicated shapes that would be difficult to manufacture using traditional processes. Sintered iron and steel products are commonly found in automotive components, machinery parts, and structural applications. Aluminum is less often subjected to traditional sintering compared to iron and steel because it has a lower melting point and higher thermal conductivity. However, with advanced techniques such as spark plasma sintering and hot pressing, aluminum powders are effectively sintered to create lightweight and corrosion-resistant parts. Titanium is sintered to produce parts that benefit from the metal’s high strength-to-weight ratio and excellent corrosion resistance. Due to its biocompatibility, sintered titanium is heavily used in medical implants and surgical devices. Metal alloys, such as brass, bronze, iron and carbon steels, iron-copper, copper steels, iron-nickel, and nickel steels, which combine two or more elements, offer enhanced properties such as improved strength and corrosion resistance tailored to meet specific industrial needs. With sintering, metal alloys are used to create products with enhanced features. Ceramics, non-metallic and inorganic, are known for their heat resistance, hardness, and electrical insulation, making them suitable for high-temperature environments. Sintering in ceramics involves heating powdered ceramic material until it binds together into a solid form. Silicon carbide (SiC) is known for its hardness, thermal conductivity, and resistance to chemical attack, requiring high sintering temperatures and additives for application in high-temperature furnaces and cutting tools. Zirconia (ZrO2), valued for its strength and resistance to wear, involves stabilizers such as yttria during sintering to prevent phase changes, making it suitable for dental implants and fuel cells. Alumina (Al2O3) is utilized for its hardness and thermal stability, with sintering processes commonly used in electrical insulators and wear-resistant components. Silica (SiO2) has a high melting point and low thermal expansion, though its sintering can be challenging due to crystallization, which is applicable in refractories and glass production. Magnesia (MgO) is appreciated for thermal conductivity and stability, usually sintered at temperatures over 1500°C for uses in refractories and thermal insulation. Beryllium Oxide (BeO) offers high thermal conductivity and electrical insulating properties, requiring controlled sintering environments due to toxicity; it’s often used in electronic components and microwave devices. Aluminum nitride (AlN) is known for thermal conductivity and electrical insulation, and sintering aids such as yttria are needed for heat sinks and electronic substrates. Composite materials are made by combining two or more different substances to create a material with properties superior to the individual components. With sintering, composites such as metal-ceramic or metal-polymer can be created.
End-User: Extensive usage of sintering processes in the automotive industry to produce modern, precise components
The automotive industry makes extensive use of sintering, particularly in the production of parts such as gears, bearings, and engine components. Sintering allows for the creation of complex shapes and high-strength materials, which are essential for the durability and performance of vehicles. In aerospace, sintering is used primarily for high-performance components that must withstand extreme stresses and temperatures. Examples include turbine blades and structural parts. The ability to fine-tune the attributes of materials through sintering makes it highly valuable in this sector. The medical sector uses sintering for the production of implants, dental prostheses, and various surgical instruments. The biocompatibility and precision of sintered parts are critically important for patient safety and effectiveness. The electronics industry uses sintering in the creation of components such as capacitors, inductors, and various types of sensors. The technique allows for the creation of small, precise, and reliable parts, essential in modern electronic devices. Various industrial applications use sintering to produce tools, machinery parts, and heavy-duty components. These industries value the method for its efficiency and the strength of the materials produced.
Porter’s Five Forces Analysis
The porter's five forces analysis offers a simple and powerful tool for understanding, identifying, and analyzing the position, situation, and power of the businesses in the Sintering Market. This model is helpful for companies to understand the strength of their current competitive position and the position they are considering repositioning into. With a clear understanding of where power lies, businesses can take advantage of a situation of strength, improve weaknesses, and avoid taking wrong steps. The tool identifies whether new products, services, or companies have the potential to be profitable. In addition, it can be very informative when used to understand the balance of power in exceptional use cases.
Market Share Analysis
The market share analysis is a comprehensive tool that provides an insightful and in-depth assessment of the current state of vendors in the Sintering Market. By meticulously comparing and analyzing vendor contributions, companies are offered a greater understanding of their performance and the challenges they face when competing for market share. These contributions include overall revenue, customer base, and other vital metrics. Additionally, this analysis provides valuable insights into the competitive nature of the sector, including factors such as accumulation, fragmentation dominance, and amalgamation traits observed over the base year period studied. With these illustrative details, vendors can make more informed decisions and devise effective strategies to gain a competitive edge in the market.
FPNV Positioning Matrix
The FPNV positioning matrix is essential in evaluating the market positioning of the vendors in the Sintering Market. This matrix offers a comprehensive assessment of vendors, examining critical metrics related to business strategy and product satisfaction. This in-depth assessment empowers users to make well-informed decisions aligned with their requirements. Based on the evaluation, the vendors are then categorized into four distinct quadrants representing varying levels of success, namely Forefront (F), Pathfinder (P), Niche (N), or Vital (V).
Recent Developments
Desktop Metal Unveils PureSinter Furnace, Advanced Solution for Cleaner, High-Purity Metal Part Production
Desktop Metal, Inc., has introduced the PureSinter furnace, designed for the debinding and sintering of metal parts produced via Binder Jetting (BJT) Additive Manufacturing, Metal Injection Molding (MIM), and Press and Sinter Powder Metallurgy (PM). Developed over five years, PureSinter boasts hot walls that prevent contamination buildup and maintains an airtight environment for efficient waste removal and high purity. [Published On: June 10, 2024]
Retech and GeniCore Collaborate to Revolutionize Powder Metal Processes with Energy-Efficient Spark Plasma Sintering
Retech, an American subsidiary of the SECO/WARWICK Group, has entered into a collaboration with GeniCore, a company specializing in composite materials engineering, to enhance its offerings in powder metal processes through Spark Plasma Sintering (SPS). SPS technology integrates pressure and thermal energy to bond materials, using less energy than traditional methods like Hot Pressing. The process involves passing a powerful pulse of electric current directly through the material in a graphite mold under vacuum, generating high temperatures via Joule heating for sinter bonding. [Published On: August 23, 2023]
New Furnace-Access Program by Tritone and DSH Enhances Sintering Flexibility without Upfront Costs
Tritone Technologies and DSH Technologies have partnered to enhance the accessibility and adoption of Tritone’s MoldJet Technology through the new Furnace-Access program. This initiative provides Tritone customers with immediate access to top-tier Elnik sintering furnaces and expert metallurgical support, eliminating the need for upfront capital investment or additional staffing. The program offers flexibility, allowing customers to outsource sintering on a long-term basis or transition to in-house operations as their needs evolve, supported by DSH’s expertise and training services. [Published On: June 15, 2023]
Strategy Analysis & Recommendation
The strategic analysis is essential for organizations seeking a solid foothold in the global marketplace. Companies are better positioned to make informed decisions that align with their long-term aspirations by thoroughly evaluating their current standing in the Sintering Market. This critical assessment involves a thorough analysis of the organization’s resources, capabilities, and overall performance to identify its core strengths and areas for improvement.
Key Company Profiles
The report delves into recent significant developments in the Sintering Market, highlighting leading vendors and their innovative profiles. These include AMES Group Sintering, S.A., ASCO Sintering Co., Catalus Corporation by Phoenix Sintered Metals, LLC, Clearfield Metal Technologies, Inc., Fine Sinter Co., Ltd., GKN Powder Metallurgy, Hitachi Ltd., Hoganas AB, JFE Steel Corporation, Kyocera Corporation, M M Sintered Pvt. Ltd., Miba AG, Nippon Steel Corporation, Plansee SE, Pometon SpA, Precision Sintered Products, PSM Industries, Inc., Sandvik AB, Singhal Sintered Private Limited, Sintercom India Ltd., Sintergy Inc., Sintering Solutions Pvt. Ltd., Sinteris S.p.A., Sintex A/S, and Sumitomo Corporation.
Market Segmentation & Coverage
This research report categorizes the Sintering Market to forecast the revenues and analyze trends in each of the following sub-markets:
- Material Analysis
- Ceramics
- Material
- Metals
- Low-Grade Alloy Steel
- Pure Iron
- Plastics
- Technology
- Laser Sintering
- Microwave Sintering
- Spark Plasma Sintering (SPS)
- Traditional Sintering
- End Use
- Aerospace & Defense
- Automotive
- Consumer Products
- Electronics
- Healthcare
- Industrial
- Research Institutions
- Region
- Americas
- Argentina
- Brazil
- Canada
- Mexico
- United States
- California
- Florida
- Illinois
- New York
- Ohio
- Pennsylvania
- Texas
- Asia-Pacific
- Australia
- China
- India
- Indonesia
- Japan
- Malaysia
- Philippines
- Singapore
- South Korea
- Taiwan
- Thailand
- Vietnam
- Europe, Middle East & Africa
- Denmark
- Egypt
- Finland
- France
- Germany
- Israel
- Italy
- Netherlands
- Nigeria
- Norway
- Poland
- Qatar
- Russia
- Saudi Arabia
- South Africa
- Spain
- Sweden
- Switzerland
- Turkey
- United Arab Emirates
- United Kingdom
- Americas
This research report offers invaluable insights into various crucial aspects of the Sintering Market:
- Market Penetration: This section thoroughly overviews the current market landscape, incorporating detailed data from key industry players.
- Market Development: The report examines potential growth prospects in emerging markets and assesses expansion opportunities in mature segments.
- Market Diversification: This includes detailed information on recent product launches, untapped geographic regions, recent industry developments, and strategic investments.
- Competitive Assessment & Intelligence: An in-depth analysis of the competitive landscape is conducted, covering market share, strategic approaches, product range, certifications, regulatory approvals, patent analysis, technology developments, and advancements in the manufacturing capabilities of leading market players.
- Product Development & Innovation: This section offers insights into upcoming technologies, research and development efforts, and notable advancements in product innovation.
Additionally, the report addresses key questions to assist stakeholders in making informed decisions:
- What is the current market size and projected growth?
- Which products, segments, applications, and regions offer promising investment opportunities?
- What are the prevailing technology trends and regulatory frameworks?
- What is the market share and positioning of the leading vendors?
- What revenue sources and strategic opportunities do vendors in the market consider when deciding to enter or exit?
- Preface
- Research Methodology
- Executive Summary
- Market Overview
- Market Insights
- Sintering Market, by Material Analysis
- Sintering Market, by Technology
- Sintering Market, by End Use
- Americas Sintering Market
- Asia-Pacific Sintering Market
- Europe, Middle East & Africa Sintering Market
- Competitive Landscape
- List of Figures [Total: 21]
- List of Tables [Total: 387]
- List of Companies Mentioned [Total: 25]
- How big is the Sintering Market?
- What is the Sintering Market growth?
- When do I get the report?
- In what format does this report get delivered to me?
- How long has 360iResearch been around?
- What if I have a question about your reports?
- Can I share this report with my team?
- Can I use your research in my presentation?