The Aero-Engine Coatings Market size was estimated at USD 1.08 billion in 2024 and expected to reach USD 1.15 billion in 2025, at a CAGR 5.66% to reach USD 1.51 billion by 2030.
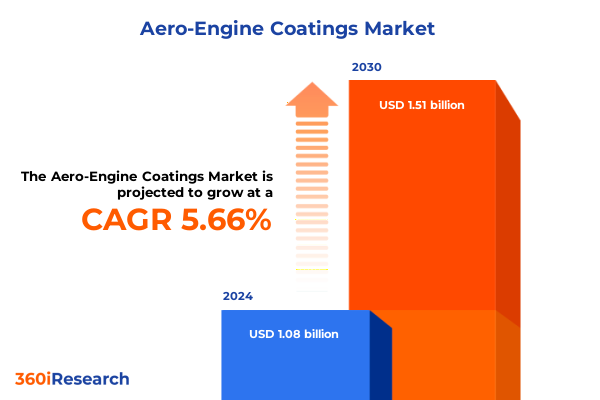
Introduction to the Evolving Aero-Engine Coatings Landscape
The aerospace industry is at a pivotal juncture where technology, performance expectations, and sustainability concerns are converging to redefine standards. In this dynamic environment, advanced coatings for aero-engines have grown in importance, addressing the perennial demands for enhanced durability, efficiency, and safety. The interplay between cutting-edge material science and innovative manufacturing processes has given rise to coatings that not only withstand the rigors of high performance but also extend service life and reduce maintenance intervals.
This comprehensive exploration delves into the factors driving change, offering a nuanced understanding of market evolution. It provides a clear perspective on emerging trends, challenges, and opportunities that influence decision-making for stakeholders across the board. As engines evolve to power next-generation aircraft, the coatings that protect and optimize these critical components must keep pace with exacting standards, ensuring that performance, reliability, and longevity are maintained in the most demanding operational environments.
This analysis sets the stage for a deeper inquiry into the transformative shifts reshaping the industry, segment-specific insights that underscore market complexity, and regional as well as corporate landscapes that highlight strategic innovations. Our narrative is crafted to offer both expert insights and a clear pathway for industry leaders to embrace change, capitalize on advancement trends, and secure a competitive edge.
Transformative Shifts Reshaping Aero-Engine Coatings
The aerospace sector is witnessing transformative shifts that are redefining the role of coatings in engine performance and reliability. Recent advancements in material sciences and surface engineering have led to the creation of coatings with superior properties such as high temperature resistance, improved oxidation protection, and overall enhanced durability.
Regulatory evolution has also played a central role. With stringent environmental and safety standards being introduced globally, manufacturers are compelled to adopt coatings that reduce emissions and enhance fuel efficiency while remaining resilient under extreme conditions. This has fostered an environment ripe for innovation, where traditional methodologies are being revisited and novel solutions are emerging to meet the dual challenges of performance and sustainability.
Convergence of digital technologies with traditional coating application methods has further accelerated these shifts. The integration of real-time monitoring, predictive maintenance, and data analytics has enabled manufacturers to optimize coating processes and perform targeted upgrades. This synergy between advanced techniques and digital insights is transforming how industry players approach maintenance cycles and operational costs, ultimately leading to safer and more efficient aero-engine operations.
In essence, the landscape for aero-engine coatings is no longer about incremental performance improvements but represents a paradigm shift where comprehensive advancements are paving the way for robust, multi-functional coatings that meet future expectations. This evolution is a call to action for industry players to invest in research and development, modernize their manufacturing techniques, and adopt innovative solutions that address both immediate challenges and long-term strategic goals.
Key Segmentation Insights in Aero-Engine Coatings
A detailed analysis of the market segments reveals a multifaceted structure that provides valuable insights into the evolving needs and opportunities within the aero-engine coatings domain. Segmenting the market based on coating type unveils categories like oxidation and corrosion protective coatings, sacrificial coatings, thermal barrier coatings, and wear resistant coatings. Each of these brings its own set of advantages, addressing various industry needs from preventing oxidation to ensuring superior shock resistance in extreme conditions.
Assessment based on base material shows that aluminum alloys, stainless steel, and superalloys each require tailored coating solutions that balance weight and strength with corrosion resistance. This implies that manufacturers must continuously adapt their formulations to cater to the unique demands imposed by diverse base materials.
When viewed through the lens of application industries, distinct sectors such as commercial aviation, industrial gas turbines, marine applications, and military aviation demonstrate specific performance and reliability requirements. The convergence of operational demands mandates coatings that can perform optimally across a spectrum of environments, ranging from commercial aircraft flight cycles to the rigorous performance standards seen in military aviation or industrial gas turbines.
The technology-driven segmentation underscores various methods including chemical vapor deposition, diffusion coatings, electrodeposition, physical vapor deposition, and thermal spray. In the case of physical vapor deposition, further scrutiny reveals specific techniques like electron-beam physical vapor deposition and sputter deposition, each contributing unique benefits in terms of deposition control and coating uniformity. Thermal spray, with its sub-segments of high velocity oxy-fuel coating and plasma spray, demonstrates exceptional versatility in addressing surface integrity and resistance to wear. This technical segmentation emphasizes the need for precision engineering in selecting appropriate coating processes based on the intended operational stressors.
Further, the market is differentiated by product form into liquid coatings and powder coatings. This distinction is critical as it speaks to differences in application methods, curing times, and overall performance outcomes, prompting manufacturers to focus on optimizing each form for maximum efficiency. Analyzing the end user segment, which primarily comprises engine manufacturers and MRO service providers, reveals that the decision-making process is highly influenced by the operational efficiencies and long-term maintenance costs associated with each coating type.
Segmentation based on the coating process itself, distinguishing between ex-situ and in-situ coatings, further highlights variations in application methods that impact both performance outcomes and production timelines. Additionally, examining coating performance characteristics such as abrasion resistance, adhesion strength, oxidation resistance, and thermal shock resistance provides a granular understanding of the functional demands placed on these protective layers.
Finally, the segmentation analysis encompasses the aspect of recoatability, contrasting multi-layer coatings with single layer coatings. This factor is crucial in understanding the strategic considerations for extensions of service life and the cost-effectiveness of maintenance cycles. Collectively, these segmentation insights illustrate a highly diverse landscape where precision and customization are paramount, necessitating an integrative approach that blends material science with engineering best practices to meet future challenges.
This research report categorizes the Aero-Engine Coatings market to analyze trends and forecast revenues across various market segments:
- Coating Type
- Base Material
- Application Industry
- Technology
- Product Form
- End User
- Coating Process
- Coating Performance Characteristics
- Recoatability
Regional Insights into the Aero-Engine Coatings Market
Regional dynamics continue to significantly influence the evolution of the aero-engine coatings market. In the Americas, market maturity is paired with ongoing investments in research and adoption of state-of-the-art technologies, which support the evolution of coating formulations for greater efficiency. The region benefits from coordinated aerospace initiatives and a strong culture of innovation that continually pushes technical boundaries.
In the combined region of Europe, Middle East & Africa, traditional expertise in metallurgy and precision engineering merges with modern digitalization trends, leading to advanced solutions that are both sustainable and performance-oriented. Companies in this region are notable for their adoption of rigorous testing and certification processes, ensuring that new coatings meet stringent international standards, thereby reinforcing the region's reputation for quality and reliability.
Asia-Pacific, meanwhile, stands out due to rapid industrial growth and a robust increase in aerospace manufacturing. The region is increasingly becoming a hotbed for new technologies and cost-efficient alternatives, spurred by substantial investments in infrastructure and innovation. This expansion is complemented by a collaborative ecosystem that harmonizes emerging trends in manufacturing with global best practices. The dynamic interplay among these regions has resulted in a highly competitive landscape where advancements in coating technology are both a response to and a catalyst for broader industry trends, paving the way for a globally interconnected market driven by innovation and quality assurance.
This research report examines key regions shaping Aero-Engine Coatings market trends, highlighting factors influencing growth and industry developments:
- Americas
- Asia-Pacific
- Europe, Middle East & Africa
Market Leaders and Key Industry Players in Coatings
In the competitive realm of aero-engine coatings, a constellation of industry leaders drives transformative change by investing heavily in innovation and process optimization. Key companies ranging from A&A Thermal Spray Coatings and Akzo Nobel N.V. to APS Materials, Inc. and Axalta Coating Systems, LLC have carved out a reputation for excellence by pioneering advanced coating technologies. Global chemical giants like BASF SE and DuPont de Nemours, Inc. continue to set benchmarks, while specialized firms such as Bodycote PLC and CASwell Inc. offer tailored solutions to meet a variety of operational challenges.
Organizations such as Chromalloy Gas Turbine LLC and Compagnie de Saint-Gobain S.A. further illustrate the diversity of expertise within the space, combining legacy know-how with modern innovations to cater to a demanding clientele. The contributions of Curtiss-Wright Corporation, CVD Equipment Corporation, and Flame Spray SpA underscore the critical importance of technological precision and quality control in an arena where performance equates to safety.
General Electric Company, H.C. Starck Solutions, and Henkel AG & Co. KGaA also play instrumental roles in not only driving research and development but also shaping industry best practices. Integral companies including Hentzen Coatings, Inc., Honeywell International Inc., and Howmet Aerospace Inc. bring additional perspectives to product innovation and market strategy. Further, entities like IHI Ionbond AG, Indestructible Paint Limited, and Lincotek Group S.p.A. demonstrate how niche specialization can yield significant advantages in addressing unique operational needs.
Other influential names such as MDS Coating Technologies Corp., Metallisation Limited, MTU Aero Engines AG, and OC Oerlikon Corporation AG are celebrated for their commitment to excellence, while PPG Industries, Inc., Praxair S.T. Technology Inc. by Linde PLC, SilcoTek, and Turbocam Inc. ensure that the market remains both diverse and innovative. These companies not only set industry standards but also foster a robust competitive environment where continuous improvement and technological disruption serve as catalysts for overall market growth.
This report provides an overview of key companies, their market share and presence, and the strategies driving competition in the Aero-Engine Coatings market:
- A&A Thermal Spray Coatings
- Akzo Nobel N.V.
- APS Materials, Inc.
- Axalta Coating Systems, LLC
- BASF SE
- Bodycote PLC
- CASwell Inc.
- Chromalloy Gas Turbine LLC
- Compagnie de Saint-Gobain S.A.
- Curtiss-Wright Corporation
- CVD Equipment Corporation
- DuPont de Nemours, Inc.
- Flame Spray SpA
- General Electric Company
- H.C. Starck Solutions
- Henkel AG & Co. KGaA
- Hentzen Coatings, Inc.
- Honeywell International Inc.
- Howmet Aerospace Inc.
- IHI Ionbond AG
- Indestructible Paint Limited
- Lincotek Group S.p.A.
- MDS Coating Technologies Corp.
- Metallisation Limited
- MTU Aero Engines AG
- OC Oerlikon Corporation AG
- PPG Industries, Inc.
- Praxair S.T. Technology Inc. by Linde PLC
- SilcoTek
- Turbocam Inc.
Actionable Recommendations for Future Industry Leaders
Industry leaders should place a premium on integrating advanced material research with scalable production methods. As competition intensifies, the importance of investing in next-generation coating technologies cannot be overstated. Companies are encouraged to:
- Forge deeper collaborations with research institutions and technology partners to co-develop innovative formulations that meet both current performance metrics and anticipate future regulatory shifts.
- Expand into niche market segments by tailoring solutions based on diverse operational needs, whether addressing specific base materials or specialized environmental conditions.
- Leverage digital transformation through the implementation of Industry 4.0 technologies, ensuring that predictive maintenance, quality control, and process automation become an integral part of the production ecosystem.
- Prioritize sustainable practices by incorporating eco-friendly materials and production methods to future-proof operations against evolving environmental regulations.
- Establish robust post-sale support networks that facilitate real-time feedback, driving continuous improvement and lower lifecycle costs.
By following these recommendations, leaders can harness emerging opportunities while mitigating the risks associated with rapid technological and market shifts. Strategic investments in research and development, coupled with dynamic operational improvements, will ensure that both traditional and emerging market segments receive the quality and innovation needed to meet today’s challenges and tomorrow’s opportunities.
Explore AI-driven insights for the Aero-Engine Coatings market with ResearchAI on our online platform, providing deeper, data-backed market analysis.
Ask ResearchAI anything
World's First Innovative Al for Market Research
Conclusion: Embracing a Future of Continual Innovation
The aero-engine coatings market is undergoing a transformation propelled by technological advancements, rigorous quality standards, and a shift towards sustainability. An integrated overview of the market segments, regional trends, and leading companies reveals a multifaceted ecosystem that is adapting rapidly to meet evolving demands. As new materials and techniques emerge, the reliance on robust research and data-driven strategies becomes essential for success.
The analysis highlights that companies which invest in advanced production methods, foster industry partnerships, and focus on targeted innovations are best positioned to thrive in an increasingly competitive landscape. By embracing a forward-thinking approach and balancing incremental improvements with bold technological leaps, stakeholders can secure long-term operational advantages and meet future challenges head-on.
In conclusion, the strides made in material science and digital integration signal a promising future where efficiency, performance, and sustainability are not mutually exclusive but rather mutually reinforcing pillars driving the next wave of industry transformation.
This section provides a structured overview of the report, outlining key chapters and topics covered for easy reference in our Aero-Engine Coatings market comprehensive research report.
- Preface
- Research Methodology
- Executive Summary
- Market Overview
- Market Insights
- Aero-Engine Coatings Market, by Coating Type
- Aero-Engine Coatings Market, by Base Material
- Aero-Engine Coatings Market, by Application Industry
- Aero-Engine Coatings Market, by Technology
- Aero-Engine Coatings Market, by Product Form
- Aero-Engine Coatings Market, by End User
- Aero-Engine Coatings Market, by Coating Process
- Aero-Engine Coatings Market, by Coating Performance Characteristics
- Aero-Engine Coatings Market, by Recoatability
- Americas Aero-Engine Coatings Market
- Asia-Pacific Aero-Engine Coatings Market
- Europe, Middle East & Africa Aero-Engine Coatings Market
- Competitive Landscape
- List of Figures [Total: 35]
- List of Tables [Total: 506 ]
Contact Ketan Rohom for Exclusive Market Research Insights
For industry stakeholders looking for deeper insights and actionable strategies in the ever-evolving aero-engine coatings market, connecting directly with a seasoned expert can be transformative. Ketan Rohom, Associate Director, Sales & Marketing, is at the forefront of this innovative landscape. With a profound understanding of market dynamics, Ketan can provide comprehensive guidance and a detailed report that unravels critical trends, segmentation analyses, and technological breakthroughs.
Engage today to learn how you can leverage this information to optimize your strategic initiatives and drive competitive advantage. Reach out to Ketan Rohom now to purchase the detailed market research report and secure a vital resource that is tailored to meet the demands of modern aero-engine coatings complexities. Your next step towards informed decision-making and operational excellence begins with this essential connection.
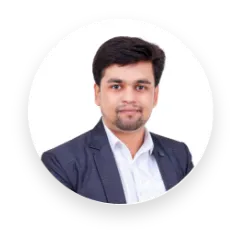
- How big is the Aero-Engine Coatings Market?
- What is the Aero-Engine Coatings Market growth?
- When do I get the report?
- In what format does this report get delivered to me?
- How long has 360iResearch been around?
- What if I have a question about your reports?
- Can I share this report with my team?
- Can I use your research in my presentation?